Agence de protection de l'environnement (EPA) reconnue
La tourbe de sphaigne est largement reconnue pour ses propriétés absorbantes exceptionnelles, ce qui en fait un matériau précieux pour la réhabilitation environnementale, notamment en cas de déversement d'hydrocarbures et de produits chimiques. Selon les directives de l'Agence de protection de l'environnement (EPA) des États-Unis, les absorbants à base de tourbe de sphaigne sont considérés comme non lixiviables et sans danger pour l'enfouissement, répondant à des critères clés tels que la procédure de lixiviation des caractéristiques de toxicité (TCLP) et le test des liquides de filtration de peinture (PFLT). Cela garantit qu'une fois que la tourbe de sphaigne a absorbé des matières dangereuses, elle peut être éliminée de manière sécuritaire et légale sans présenter de risques environnementaux secondaires.
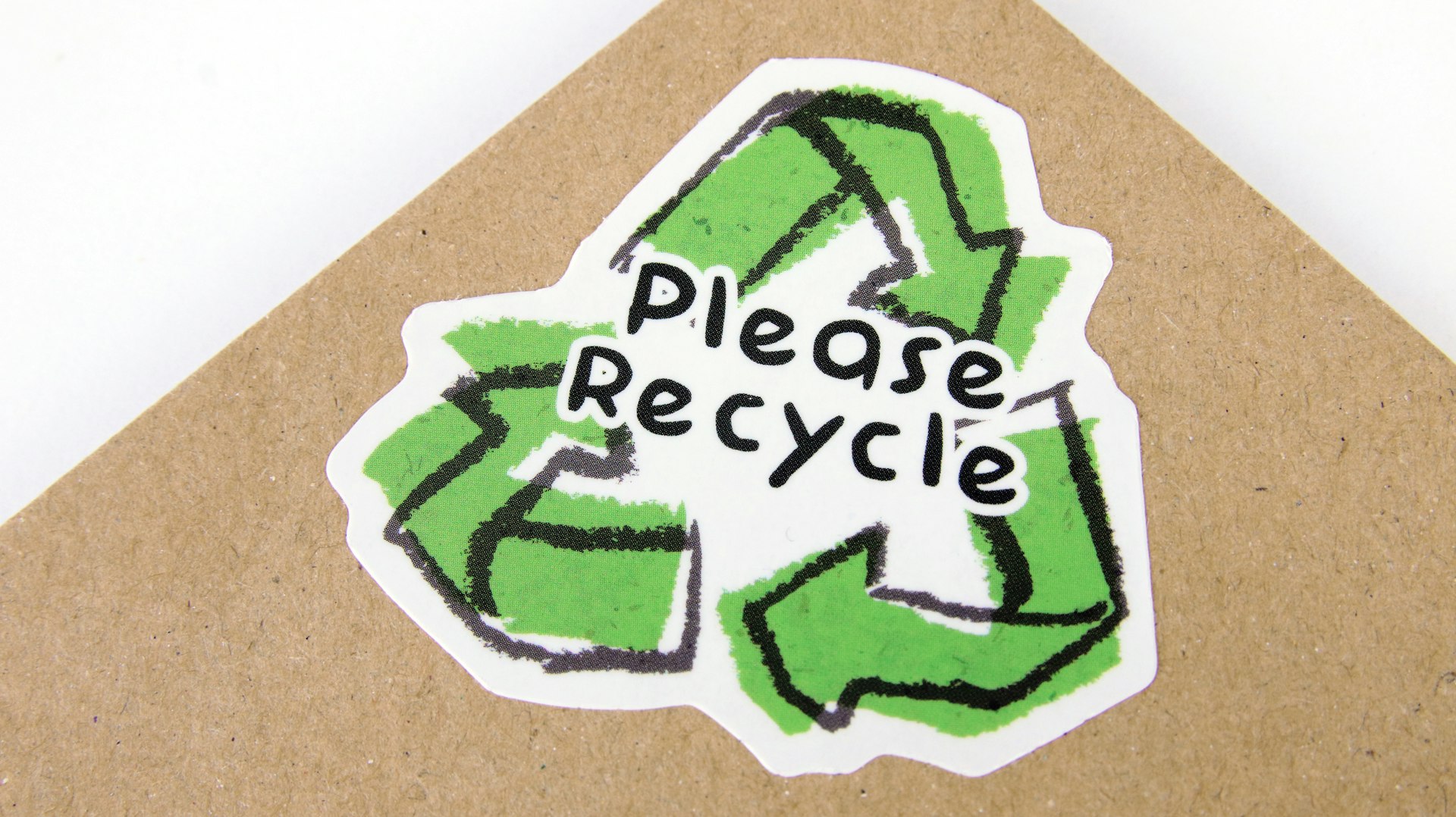
Au Canada, la réglementation environnementale de la tourbe de sphaigne relève d'Environnement et Changement climatique Canada (ECCC) et de la Loi canadienne sur la protection de l'environnement (LCPE).
Les agriculteurs canadiens qui récoltent de la tourbe de sphaigne sont soumis à des programmes de gestion environnementale stricts, notamment des plans de développement durable, des évaluations d'impact écologique et des exigences de restauration des terres après récolte. Cette réglementation garantit que l'extraction et l'utilisation de la tourbe contribuent aux objectifs de conservation environnementale à long terme.
En s'alignant sur les cadres réglementaires américain et canadien, les absorbants à base de tourbe offrent une solution sûre, durable et conforme aux normes d'enfouissement pour le nettoyage des déversements industriels et la protection de l'environnement.